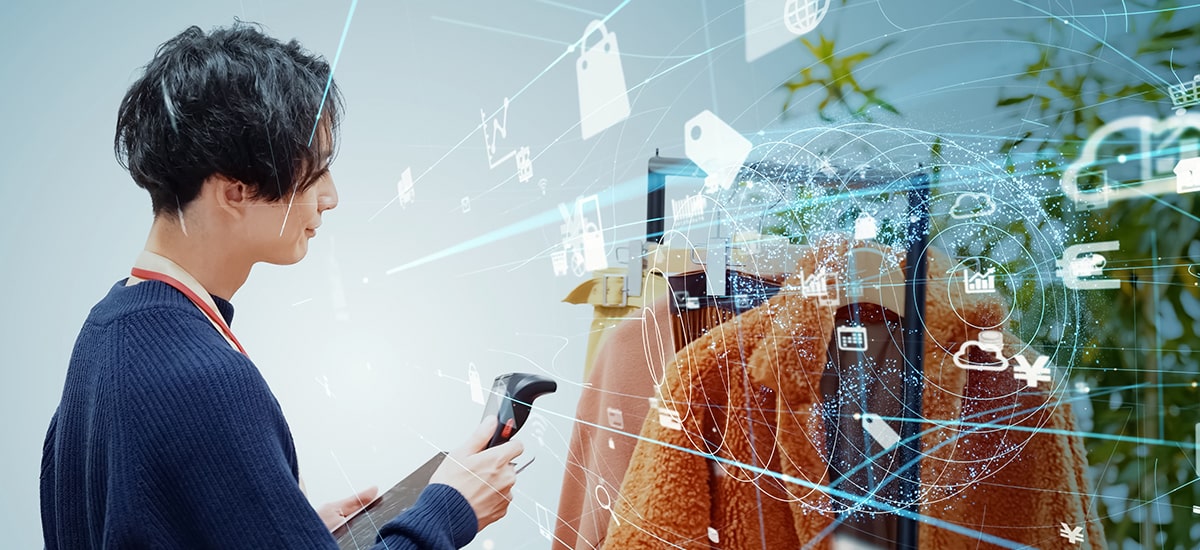
Listen to this blog
5 Ways HauteLogic Can help you Optimize Inventory Levels
With ongoing supply chain disruptions, it becomes vital for fashion, apparel, and footwear organizations to streamline their inventory by leveraging an intuitive apparel management software.
Inventory optimization is the process of maximizing the value of an organization's inventory while minimizing the costs associated with managing that inventory. It's an essential aspect of operating company assets because inventory is typically one of the largest investments a business makes, and optimizing it can directly impact its profitability. This can be achieved through an apparel inventory management software.
Why does inventory optimization matter for Fashion, Apparel, and Footwear Organizations?
One of the main reasons why inventory optimization is crucial is that it can help prevent common inventory problems like stock shortages and excess inventory. Stock shortages can be costly for a business, resulting in lost sales, decreased customer satisfaction, and missed opportunities to generate revenue. On the other hand, excess inventory can tie up valuable capital, take up valuable space, and lead to obsolescence or spoilage of products, all of which can negatively impact a company's bottom line.
By keeping an eye on stock levels and knowing how many of each SKU (Stock Keeping Unit) a business has at any given time, companies can better manage their inventory and avoid these common problems. This can involve using inventory management software to track stock levels in real-time, forecasting demand to ensure that the right amount of inventory is on hand, and implementing strategies like just-in-time (JIT) inventory management to minimize waste and improve efficiency.
In addition, optimizing inventory involves finding the right balance between the cost of holding stock (e.g., storage, insurance, obsolescence) and the cost of stockouts (e.g., lost sales, dissatisfied customers, rush orders).
Here’s how HauteLogic can optimize your fashion, apparel, and footwear organization’s inventory levels:
1. Leverage demand forecasting
The goal of inventory optimization is to strike a balance between maintaining enough inventory to meet customer demand while minimizing the costs associated with holding excess inventory. Demand forecasting plays a critical role in this process by providing insight into expected demand levels and patterns. Forecasting demand as accurately as possible allows you to reduce the amount of safety stock you need to keep on hand and develop a reliable forecast using historical sales data, market trends, and customer feedback.
By accurately forecasting demand with apparel management software, organizations can make more informed decisions about when to order inventory, how much to order, and where to store it. This can help minimize the costs associated with excess inventory while ensuring that there is enough inventory to meet customer demand.
2. Set appropriate reorder points with an apparel management software
The reorder point is the inventory level at which you need to place a new order. Setting the reorder point at the appropriate level is crucial for inventory management as it helps minimize the risk of stockouts while also reducing the need for excess inventory.
By setting the reorder point too high, a business may end up with excess inventory, leading to higher carrying costs and potential waste. On the other hand, setting the reorder point too low may result in stockouts, leading to lost sales and dissatisfied customers. In addition to determining the appropriate reorder point, businesses may also use safety stock to further minimize the risk of stockouts.
Safety stock is the extra inventory held beyond the expected demand to cover unexpected demand or lead time variability. By combining the appropriate reorder point with safety stock, businesses can maintain optimal inventory levels and provide excellent customer service while minimizing inventory carrying costs.
3. Dynamics 365 Supply Chain Management and Time-Phased Inventory Availability
Time-Phased Inventory Availability is a crucial inventory management feature in Dynamics 365 Supply Chain, which HauteLogic leverages to optimize supply chain processes. This ERP fashion software enables businesses to plan and manage their inventory levels based on forecasted demand and expected supply over a given period.
With time-phased inventory availability, businesses can view their inventory levels for each item at any point in time and adjust them based on anticipated demand. This allows them to ensure that they have the right amount of inventory on hand to meet customer demand while avoiding overstocking or understocking.
Dynamics 365 Supply Chain uses a time-phased approach to inventory availability by creating a snapshot of the inventory levels at the start of each period (usually a day or a week). This snapshot takes into account all inventory transactions that have occurred up to that point, such as sales, purchase orders, and transfers between locations.
The system then calculates the expected inventory levels at the end of each period based on anticipated demand and supply, using various algorithms such as reorder point planning, safety stock planning, and master planning. This information is then presented to users through reports and dashboards, allowing them to make informed decisions about inventory management.
Overall, time-phased inventory availability is a powerful tool for businesses to optimize inventory levels, reduce costs, and improve customer service.
4. Conduct regular inventory audits
Regular inventory audits can help you identify slow-moving or obsolete inventory, allowing you to reduce excess stock and free up valuable warehouse space. It will also help you to ensure compliance and identify potential loopholes that can be avoided further down the road. In addition, inventory management software significantly enhances the efficiency and effectiveness of stock-related procedures while streamlining inventory audits for more precise results. This will help businesses improve time efficiency and minimize the risk of errors.
5. Use an apparel inventory management software
Inventory management software can help you track inventory levels in real time, automate reorder processes, and generate reports that can inform your inventory optimization strategy. The best way to go about this is leveraging apparel management software that offers a holistic solution that fast-tracks processes and ensures that your PLM cycle is always on track.
By implementing these strategies and regularly reviewing and adjusting your inventory management practices, you can optimize your inventory levels and reduce the risk of stockouts while minimizing holding costs.
Get in touch with our experts to learn more.